A-XPF
Most tapping troubles are caused by unstable chip evacuation. The A-XPF forms threads by plastic deformation of the work material and does not generate cutting chips. The A-XPF enables the reduction of tool change time caused by cutting chip troubles and machine downtime required for removing accumulated cutting chips. Furthermore, by enabling stable and uninterrupted machining, power consumption can be reduced, which minimizes environmental impact. Large diameter sizes of M18 to M24 can also accommodate the machining of large components. The A-OIL-XPF with internal coolant holes is compatible with mist machining. Mist coolant cutting eliminates the need for oil disposal, which helps reduce waste. Furthermore, there is less scattering of cutting oil, which also leads to an improved work environment.The product lineup has been expanded to include a long shank type and a deep hole long shank type, specifically designed for deep hole machining applications. Thread forming taps, which operate through plastic deformation and do not generate chips, are particularly well-suited for machining small-diameter threads and extended thread lengths.
Features
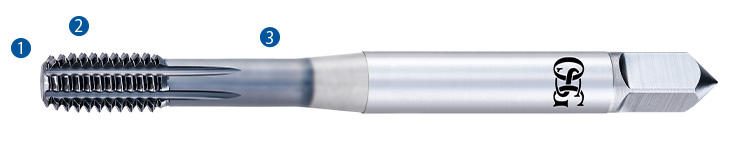
Improves productivity with zero cutting chips.



- New generation synchronized tap holder designed to maximize the performance of your A-XPF tools
Applications
Low Carbon Steel・Medium Carbon Steel・High Carbon Steel・Alloy Steel・Hardened Steel(25~35HRC)・Cast Steel・Copper・Brass・Brass Casting・Aluminum Rolled・Aluminum Alloy Casting・Zinc Alloy Casting
Lineup
Basic form
- M1~M24
With internal coolant holes
- M5~M16
Long shank
- Basic form M3~M12
- For deep holes M2~M6
Data
Achieves cutting speed of 30m/min in high-hardness material
Achieves high-speed and stable machining in SCM440(30 HRC)
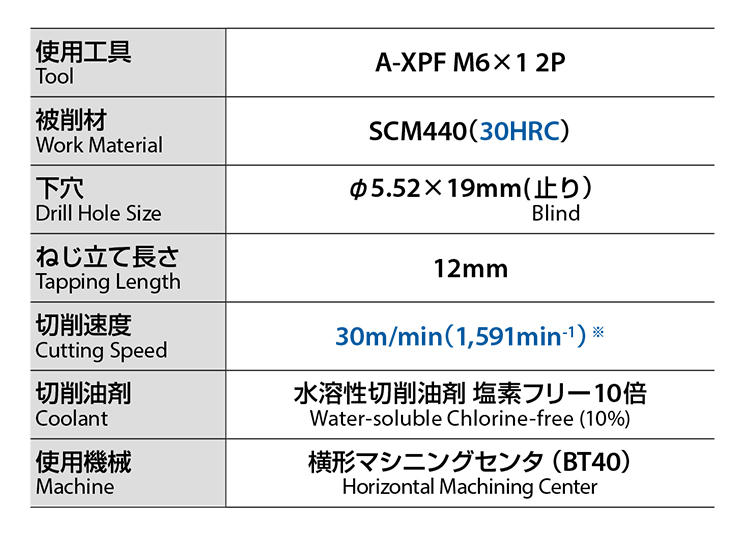
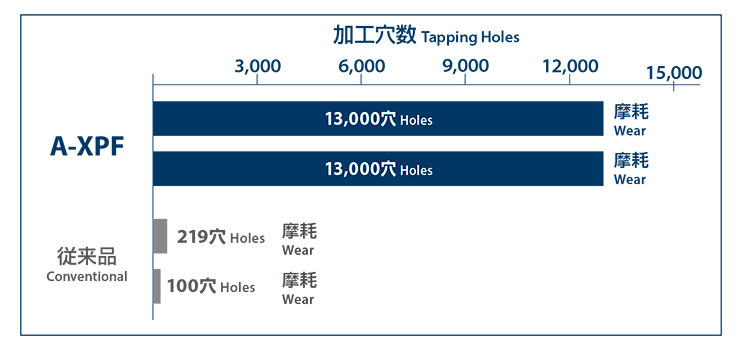
※For testing purposes, the conventional product was also used under high-speed cutting condition.
Environmental Considerations
Compatible with mist coolant processing to reduce waste
Mist coolant cutting eliminates the need for waste oil disposal, which helps reduce waste. Furthermore, there is less scattering of cutting oil, which also leads to an improved work environment.
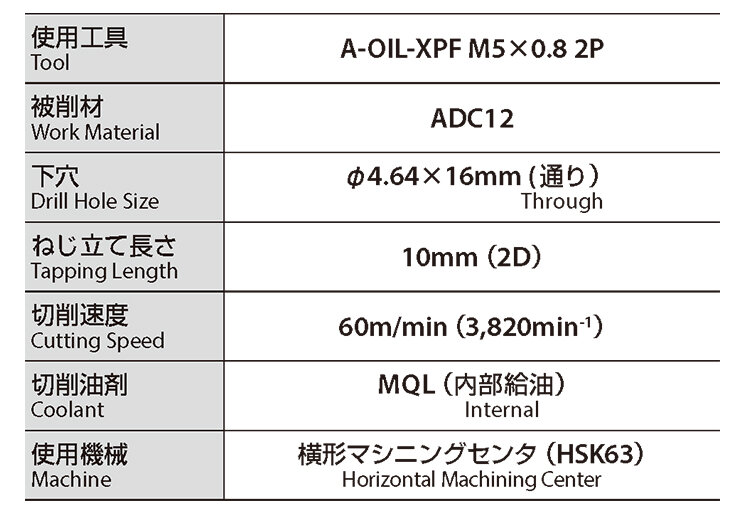
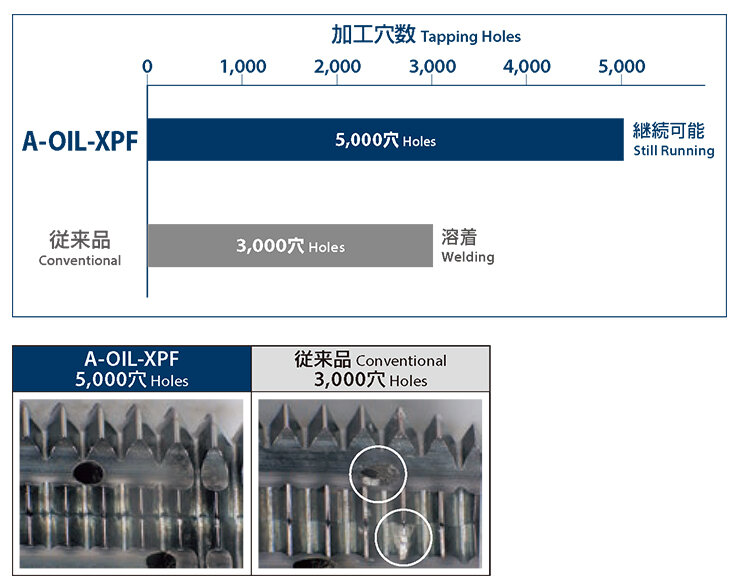